What Else Could an Engineer Want?
- Allyson Lacoste
- Jun 26, 2017
- 2 min read
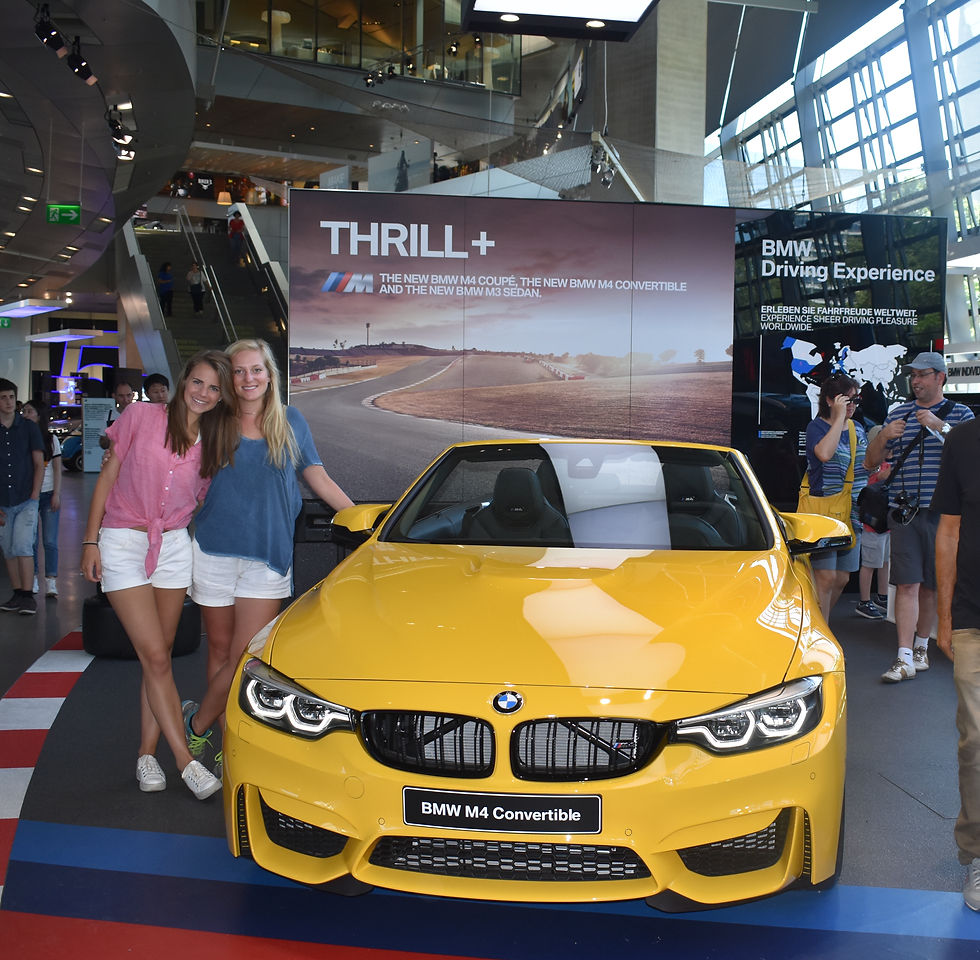
My friends and family at home don’t always understand why factory tours are some of my favorite parts of this trip. They, of course, assume it’s because I’m an engineering major, so I must like “nerdy” things like that. But let me promise you one thing, you do not have to be an engineering major to enjoy and appreciate the work that goes on in these places of manufacturing. The magic of the assembly line work is clear, and it is easy to understand just how much detail is put into the cars driven everyday! Plus, I also learn tons of mind-blowing facts along the way. We have been fortunate enough to tour two car manufacturers on this trip, Volkswagen and BMW, and both have been some of the highlights of my time here.
Today, we were taken on an in depth and close up look at the BMW factory in Munich. Our tour guide was wonderful, as he easily explained the inner workings of the factory so that we all understood each aspect. From a civil engineering perspective, I loved the iconic BMW building, which was built by an Austrian architect with the influence of nature and its elements in mind. We were taken to the press shop, body shop, paint application, where they make the engines, the assembly line, and final testing areas through what seemed like a winding maze up, down, and all over the premises. I loved learning about BMW’s unique creation of each car. Each one is customized to the client’s order, but only once it reaches the assembly line. This is one of the many efficient ways BMW keeps their lines running smoothly; every car is handled and made the same way, no matter the details for the customer or country, until it reaches the assembly line. Another way they keep their plant running smoothly is by having what they call a “buffer.” This buffer of parts to fully assembled frames sustains the rest of the line, and keeps it in motion if one section has to be temporarily shut down. The quality control here is also top notch; they take pictures of the cars at multiple times to compare for quality assurance, as well as randomly pull cars from the assembly line to do further testing. They also do many driving tests on each and every car. Our tour guide also told us about new technologies they are implementing in what they call Industry 4.0. These include things like smart watches that know which piece an assembly line worker is installing, and gloves with a “sixth finger” that will decrease strain in workers’ hands. The plant is also undergoing renovations to increase their car capacity from 900 to 1,400 cars produced everyday.
After the tour was over, we were given an hour to explore the cars they had on display. This was so much fun! We took lots of pictures and acted like the crazy tourists we were!

Comments